Understanding the Fundamentals and Applications of Plastic Extrusion in Modern Production
In the realm of modern-day manufacturing, the strategy of plastic extrusion plays a critical role - plastic extrusion. This complex procedure, including the melting and shaping of plastic through specialized passes away, is leveraged across numerous industries for the development of varied products. From vehicle components to customer items packaging, the applications are vast, and the capacity for sustainability is equally impressive. Unraveling the basics of this process discloses real adaptability and capacity of plastic extrusion.
The Basics of Plastic Extrusion Refine
While it might appear complicated, the principles of the plastic extrusion process are based upon reasonably straightforward concepts. It is a manufacturing process where plastic is melted and after that shaped into a constant account with a die. The raw plastic product, often in the kind of pellets, is fed into an extruder. Inside the extruder, the plastic undergoes warmth and pressure, causing it to thaw. The molten plastic is after that required via a designed opening, recognized as a die, to create a long, constant product. The extruded product is cooled down and after that cut to the preferred size. The plastic extrusion procedure is extensively used in numerous markets due to its cost-effectiveness, flexibility, and performance.
Various Types of Plastic Extrusion Techniques
Structure upon the basic understanding of the plastic extrusion procedure, it is necessary to check out the different techniques included in this production technique. In contrast, sheet extrusion creates huge, level sheets of plastic, which are commonly more processed right into products such as food product packaging, shower drapes, and auto parts. Recognizing these techniques is essential to utilizing plastic extrusion effectively in modern-day manufacturing.
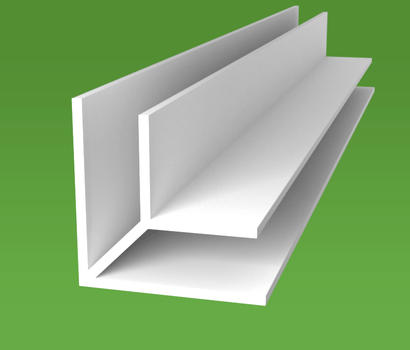
The Role of Plastic Extrusion in the Automotive Sector
A frustrating majority of components in modern cars are products of the plastic extrusion procedure. Plastic extrusion is primarily made use of in the production of different car components such as bumpers, grills, door panels, and dashboard trim. Hence, plastic extrusion plays an essential duty in automobile manufacturing.

Applications of Plastic Extrusion in Durable Goods Production
Beyond its substantial effect on the vehicle market, plastic extrusion proves just as effective in the realm of customer items manufacturing. The convenience of plastic extrusion allows makers to develop and generate complicated forms and dimensions with high accuracy and effectiveness. The flexibility, flexibility, and cost-effectiveness of plastic extrusion make it a recommended selection for numerous customer items makers, contributing substantially to the industry's growth and technology.
Ecological Impact and Sustainability in Plastic Extrusion
The pervasive use plastic extrusion in producing invites scrutiny of its eco-friendly ramifications. As a procedure that regularly makes use of non-biodegradable products, the environmental impact can be considerable. Energy intake, waste manufacturing, and carbon exhausts are all problems. Industry innovations are enhancing sustainability. Efficient equipment lowers power use, while waste monitoring systems recycle scrap plastic, reducing raw material needs. In addition, the development of biodegradable plastics offers a much more eco-friendly choice. this link In spite of these renovations, additionally technology is required to alleviate the ecological impact of plastic extrusion. As culture leans towards sustainability, makers must adjust to stay feasible, emphasizing the value of continual research study and development in this field.
Final thought
To conclude, plastic extrusion plays a critical duty in modern-day production, particularly in the vehicle and durable goods fields. Its flexibility allows for the production of a variety of parts with high precision. Its capacity for recycling and advancement of biodegradable materials uses a promising method in the direction of sustainable techniques, consequently attending to ecological issues. Understanding the essentials of this process is key to maximizing its applications and benefits.

The plastic extrusion process is extensively used in numerous markets try here due to its cost-effectiveness, adaptability, and performance.
Structure upon the basic understanding of the plastic extrusion process, it is necessary to explore the numerous methods included in this manufacturing method. plastic extrusion. In comparison, sheet extrusion develops big, flat sheets of plastic, which are normally more processed right into products such as food packaging, shower drapes, and automobile components.An overwhelming bulk of over here components in modern-day automobiles are products of the plastic extrusion procedure